Is Modular Actually Cheaper or Faster Than Components?
Originally Published by: VCReporter — June 9, 2021
SBCA appreciates your input; please email us if you have any comments or corrections to this article.
Pictured: The kitchen and living room section of a modular home is placed at a building site in the Ondulando neighborhood in Ventura on May 27, 2021. Photo by Kimberly Rivers.
In the mid-afternoon of May 27, the homeowner* of a house on Via Cielito in the Ondulando neighborhood did a walk-through of their new home. Just five hours before, only a finished foundation was in the location from which they now surveyed the view out the glass slider from the master bedroom.
The original home, which they had lived in for 30 years, was claimed in a matter of hours by the Thomas Fire in 2017. Remarkably, the new home was situated in place — albeit not fully ready to be occupied — in a similar fashion, thanks to the ingenuity of the construction company and the modular design of the home.
The project could point the way forward for other rebuilds, particularly in areas ravaged by wildfires.
The first section is placed on the foundation at the modular home build site in Ventura. May 27, 2021. Photo by Kimberly Rivers.
Ventura’s Ondulando neighborhood was hit hard by the Thomas Fire, which skipped and jumped across the canyons, claiming some homes and leaving others. Today, there are still many empty, flat lots. On some properties a masonry fireplace or empty pool are all that remain, waiting for rebuilding to begin or a buyer. Others are simply in insurance claim and/or permitting limbo.
On Via Cielito where this project took shape, a neighboring home had sold and was slated to change hands on the day of the Thomas Fire. The furniture had been moved out. Today an outdoor fireplace and seating area are all that remain. The property provided an ideal vantage point to watch the enormous crane place four sections of a modular home into place.
“We’ll have the house watertight by the end of the day,” said Rodney Tate of Camarillo-based Tate Construction and Development. Tate served as the subcontractor in charge of placing the four modular home sections in place upon the built foundation.
Martin Prideaux, of Oak View-based MPX Construction, is the general contractor for the build and met the homeowner shortly after the fire. Following issues with architects and a “low ball” budget from the insurance company (which would not cover the rebuild) Prideaux persuaded the homeowner to go modular.
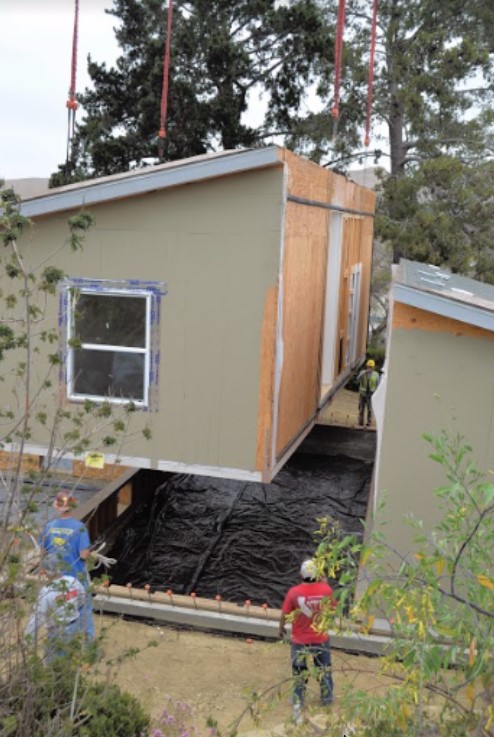
The second section is carefully placed with ground crews monitoring at the modular built site. May 27, 2021. Photo by Kimberly Rivers.
Tate said he’s done several modular home placements in Ventura County, including some in the same neighborhood. He says it’s really a better way to build a house. Traditional construction means that a home in the process of being built is “exposed” to the elements during construction. A home built inside a factory is protected during all phases, and doesn’t see the light of day until the roof is finished.
The home selected came from Redlands-based Hallmark-Southwest, which was recently purchased by Dvele, a company that has built at least one other modular home in the Ondulando neighborhood.
FROM FOUNDATION TO WALK-THROUGH IN A DAY
Modular homes are built in sections. Each section is constructed on and bolted to a steel frame, which is also the transport trailer. Once sections have been transported to the build location, steel straps from the crane are put in place and the bolts are removed.
The Via Cielito modular home is different from the one that was lost. Whereas the previous house was two stories, the new home is single story and about 100 square feet smaller, at 2170 square feet, with a 480-square-foot garage plus a storage-wine cellar. The new home has three bedrooms and two bathrooms with a powder room.
Prideaux’s company built the foundation for the four-section modular home. It will also build a custom garage and front porch sitting area, and install custom flooring and custom tile showers. Smooth stucco and decorative hardscape features will be placed on the exterior.
The placement of a modular home requires a dedicated crew and careful coordination.
On the day of installation, the crane arrived at around 7 a.m. and was operating two hours later, after being leveled and properly braced. Large round platforms were placed under each foot of the crane for stabilization.
The operator, called the pilot, of the crane communicated closely with his team member on the ground who spoke into a small handheld transmitter, giving specific instructions on first lifting the modular home section off the trailer it arrived on, and then moving the section into place. As the section lifted off the trailer, the crane slowly rotated, and ground crew members held lines attached to corners of the section. Precise directions were relayed to the pilot to ensure the section remained balanced, and lined up perfectly. Large metal levers helped shimmy it into place.
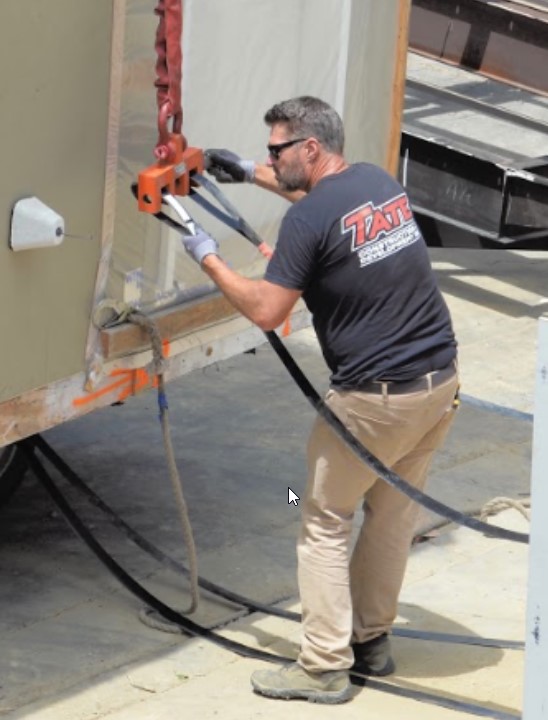
Rod Tate, of Tate Construction and Development attaches the steel straps to the “knuckle” on the crane strap at the modular home build site in Ventura. May 27, 2021. Photo by Kimberly Rivers.
The section containing the kitchen and living room was the largest, weighing in at 25,000 pounds.
As the crane lifted it, the pilot was quickly told to stop.
The weight of the wood cabinets and granite counter tops at one end made that end heavier, and the section needed to be balanced to be placed properly and ensure it did not slide in the steel straps used to attach it to the crane.
Tate’s crew went to work shifting some rolls of carpeting and carpet padding from the middle of the section to the end opposite the kitchen to try and counterbalance the kitchen. More weight was still needed, however, so buckets of heavy material were grabbed from the site and placed in the living room. After resetting the straps, the section was properly balanced and could be moved and placed on its foundation.
The only other hiccup of the day was when the final section didn’t seem to want to detach from its metal trailer frame. The crew checked for any steel bolts still attached to the trailer. Finding none, the pilot was instructed to slowly lift. It came off with a gentle pop.
The home isn’t completely finished. Tate explained that the crew will return to attach the sections to the foundation, and will make adjustments as needed for precise placement and to minimize any gaps. The largest visible gap during the first walk through was approximately 0.75 inches between the floors of the sections.
The homeowner seemed pleased but guarded with their new home during the walk-through. It can be overwhelming for the structure to take shape after waiting so long.
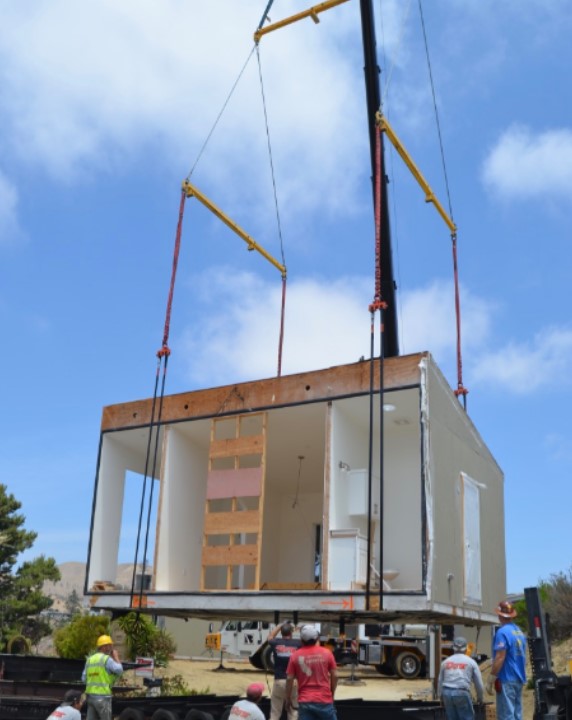
The fourth and final section of the modular home is lifted from the trailer base. May 27, 2021. Photo by Kimberly Rivers.
PERMITS AND FINANCING
Prideaux describes the permitting process with the city of Ventura as 3 ½ years of “jumping through hoops,” which caused the built home to sit for a year in the factory in Bakersfield. According to Prideaux, discrepancies between local and state permitting requirements also caused confusion. The manufacturer of the home gets the plans approved by the state but then the local entity, in this case the city of Ventura, has to issue the local building permits.
Prideaux said the process “changed dramatically” after the fires and the city seemed “overwhelmed.” Then the pandemic hit. He added that all manufactured homes are built to the same building codes as homes built onsite.
At this point the Via Cielito modular house itself is signed off already. A city inspector will only need to sign off on the garage that will be built.
When asked about the length of permitting time with the city, Prideaux said it seemed that “they weren’t sure what the state regulations were, but the state overrules the city.” With the garage and front entry being constructed on site, “we have to get a second” and separate approval “for that, then combine them all.” He said the city seems to be starting to “loosen up” with processing modular homes, which to him makes sense. Two sets of plans had to be created for the state and the city. “They are built the same way as a regular house, two-by-fours and two-by-sixes, joists . . . it’s strong.” Prideaux was impressed to not see any cracks or other signs of shifting from transport.
He had never done a modular home of this type before and wondered “can I pull this off? . . . I’d never done one before but had seen the modular homes . . . They are built like a regular house, all wood . . . I thought, ‘let’s give it a go.’ To frame this now it would cost me $500-$600 a square foot to finish.”
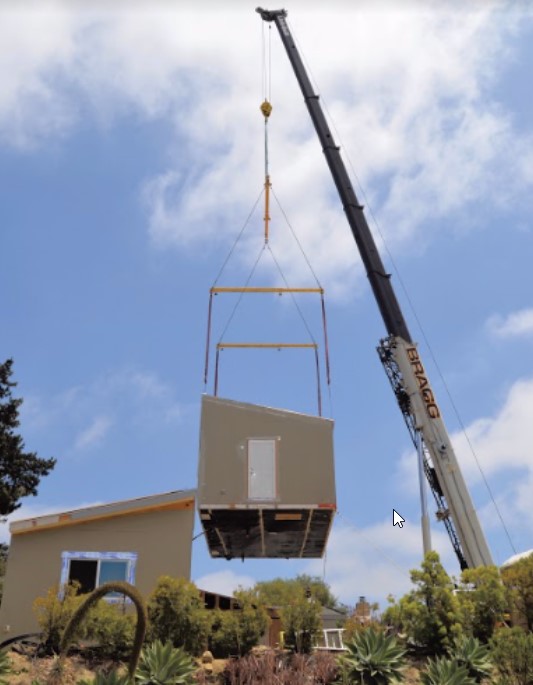
The final section is lifted by the Bragg crane and lowered into place on the foundation. May 27, 2021. Photo by Kimberly Rivers.
The sections were delivered the day before the crane arrived and the cost for transport, including a police escort for the wide loads, was $15,000. Prideaux estimated that by going with a modular construction, he was able to save the homeowner about $300,000 to $400,000. The finished cost of the house as designed will be $900,000.
“The cost of materials went up about 120%. If I had to build this [with traditional on site construction] it would be around $1.3-$1.4 million,” said Prideaux.
The lower cost, said Prideaux, is due partly to the cost of factory labor. He said they can pay minimum wage because in the factory they are cutting blocks of wood. “Out in the field they are carpenters, there is a cost difference.”
MODULAR BUILDING NORMALIZED
Every industry experiences changes with shifts in technology and consumer demand. The building trades are no different. Modular home construction has been knocking on the door of the residential construction industry for a while now, and some market areas have been resistant. But this type of building saw an uptick in Ventura County in the aftermath of the Thomas Fire.
The burst of post-Thomas rebuilds caused a strain on supply chains (compounded by the pandemic), a boom in the construction industry and a backlog in planning departments as permit requests came rolling in. This coupled with the state mandates for cities and counties to have ample housing to meet demand means that now might be the time for homeowners, builders and permit departments to iron out any kinks in the permitting system to incorporate all housing options and building processes into the mix.
When asked if there is resistance in the construction trade to this type of building, he said yes, there “sort of is resistance. People have a bad taste in their mouth” around modular homes. Some think they are ugly. Others worry that they’ll resemble mobile homes in a trailer park. But Prideaux thinks that stigma can change: Modular homes are in fact being custom designed for the homeowner and the attractive final product is changing the way people, and cities, view modular construction.
“This may be the future of building,” he stated.
Prideaux worked with the homeowner to customize the design and add various features, including solar tubes,to increase natural light, high-end granite countertops and a see-through double-sided fireplace between the living room and the backyard area. The rooms are spacious and several arched entryways added to the custom feel. Even at the unfinished phase, the home does not feel cookie cutter.
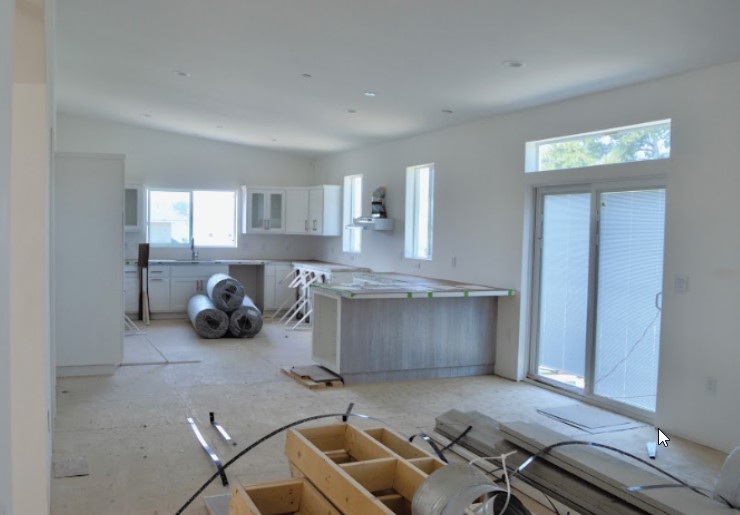
The kitchen and living room section during the walkthrough on May 27, 2021. Photo by Kimberly Rivers.
Within a stone’s throw on the same street, six homes had been claimed by Thomas. Three have been rebuilt. Two, including the neighboring home, are still flat lots. A home just across the street is under construction and nearly fully framed. In the time it took the modular home to go from a completed foundation to walk-through, the roof trusses across the street were delivered and about half nailed into place.
Prideaux estimated that the rebuild across the street would need another 10 months to get it to where the modular build is today. That home still needs to be plumbed, wired, insulated; walls inside and out finished; and windows, floors, surfaces, finishes and fixtures installed.
The modular home needs about three more months, said Prideaux, to be move-in ready. Tile, carpeting and fixtures, like faucets, still need to be installed. But the master bathtub was in place and looked inviting. If the permitting process had gone more smoothly, the modular home would have taken a total of about five to six months from grading to move in.
IS MODULAR BUILDING FASTER?
According to Peter Gilli, community development director for the city of Ventura, three Thomas Fire rebuilds in city limits have been for “modular or prefab homes.”
He pointed out in a June 7 email to the Ventura County Reporter that even with this type of construction, “all work related to the site, grading and foundation remains. And for properties with topography, which most of the Thomas Fire rebuild sites have, the site engineering is often more time consuming than the plan review of the house itself.”
“A house being designed for a site can often be easier to work into a site with topography than a pre-designed home,” Gilli continued. “An architect can be more flexible with the house to meet site constraints. A pre-designed home is what it is.”
When asked about changes to permits following massive wildfires, as mentioned by Prideaux, Gilli noted that this is an additional step requiring a state review for homes being rebuilt in high-fire areas.
In a review of city records, Gilli stated that the three modular/prefab Thomas Fire rebuilds took eight months, nine months and 18 months from “submittal date to permit issuance.” After the city provides comments on the design to the architect, it’s typical for a response from the architect to take several more months.
“Based on our information, the time frame for modular or prefab is not longer than usual,” said Gilli. “The issue is likely that owners went into doing a modular or prefab thinking it would be faster.”
As for this project being faster and less expensive than traditional onsite construction, the homeowner said that remains to be seen.
*The homeowner gave permission to photograph the construction and otherwise describe the process but wished to remain anonymous.