Site-Built 3D Printed House Will Use Wood Roof Trusses
Originally Published by: Richmond BizSense — June 23, 2021
SBCA appreciates your input; please email us if you have any comments or corrections to this article.
The 3D printer that will create the exterior of a new home being built at 217 Carnation St. is set up at the job site. (Noah Daboul photos)
Armed with a grant from a state housing agency, a group that includes a team from Virginia Tech, a Richmond construction company and two local nonprofits are trying out a new way to build and sell a home.
The venture is taking shape on a vacant Southside parcel at 217 Carnation St., where the end result will be a nearly 1,600-square-foot residence, the exterior bones of which will be made by a 3D printer. The group says it will be first home of its kind for sale in Virginia.
The project is made possible by Virginia Housing (formerly Virginia Housing Development Authority), which announced a $500,000 grant to help secure the specialized device, which prints with concrete. It’s one of only two in the U.S., the other being in Florida.
The grant was awarded to Virginia Tech’s Virginia Center for Housing Research.
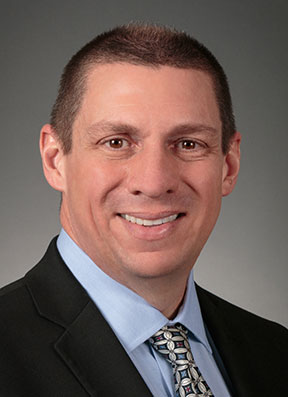
Chris Thompson
Chris Thompson, director of strategic housing at Virginia Housing, said the agency was first introduced to 3D printing at a conference a few years ago and they became interested in finding ways to use the technology.
The agency later created an innovation grant program that would help them look for partners with cutting edge ideas that would aid in construction. That’s how the connections were made to get the Richmond project going.
“We have been looking for ways to spur innovation and address the critical shortage of inventory, both for home ownership and rental,” said Thompson. “We really got intrigued by this notion of using this for the construction process. From there we entered conversations and did some more exploration, partnered with some Virginia experts in housing and research, and that brought us to where we are today.”
Copenhagen-based COBOD is the manufacturer of the large-scale 3D printer, one of which was purchased for $350,000 by Alquist 3D, a 3D printing construction company that focuses on lowering construction costs.
Virginia Housing was introduced to Alquist 3D through researchers at Virginia Tech who were working with Alquist as part of the grant from Virginia Housing. Alquist and Virginia Tech had reached out to the company to check out the costs and later used Virginia Housing’s resources to purchase the equipment.
The printer works like any other 3D printer, except it prints with concrete and is on a larger scale. Thompson said that they have a cement mixer nearby that feeds into a printer head that is mounted on a steel frame measuring about 40 feet by 40 feet. The printer head is mounted on a middle beam that moves vertically and horizontally.
“You’re basically plugging in a design into a computer system; it’s not manual, it’s all automated,” said Thompson. “It’s printing concrete around layer by layer and it stacks up to the wall height that you’re looking for. It almost looks like if you’re squeezing a tube of toothpaste, as each layer is set it begins to cure and it continues to go up and up.”
The 3D printer is being used for the wall construction for the pilot project. Thompson said that they are still going to have to go in and manually do drywall, porch construction, truss systems and other parts of the home. They are just building the skeleton of the house for this project, but plan to increase the use of the printer on other projects.
“The printed material is very durable and energy efficient. Using the technology really opens the door in terms of creativity and home design,” said Thompson. “It can be adjusted to the lot sizes and can be programmed to marry in with the existing neighborhood and retain some of the character. It also saves time. We can do the wall systems in 14-15 hours.”
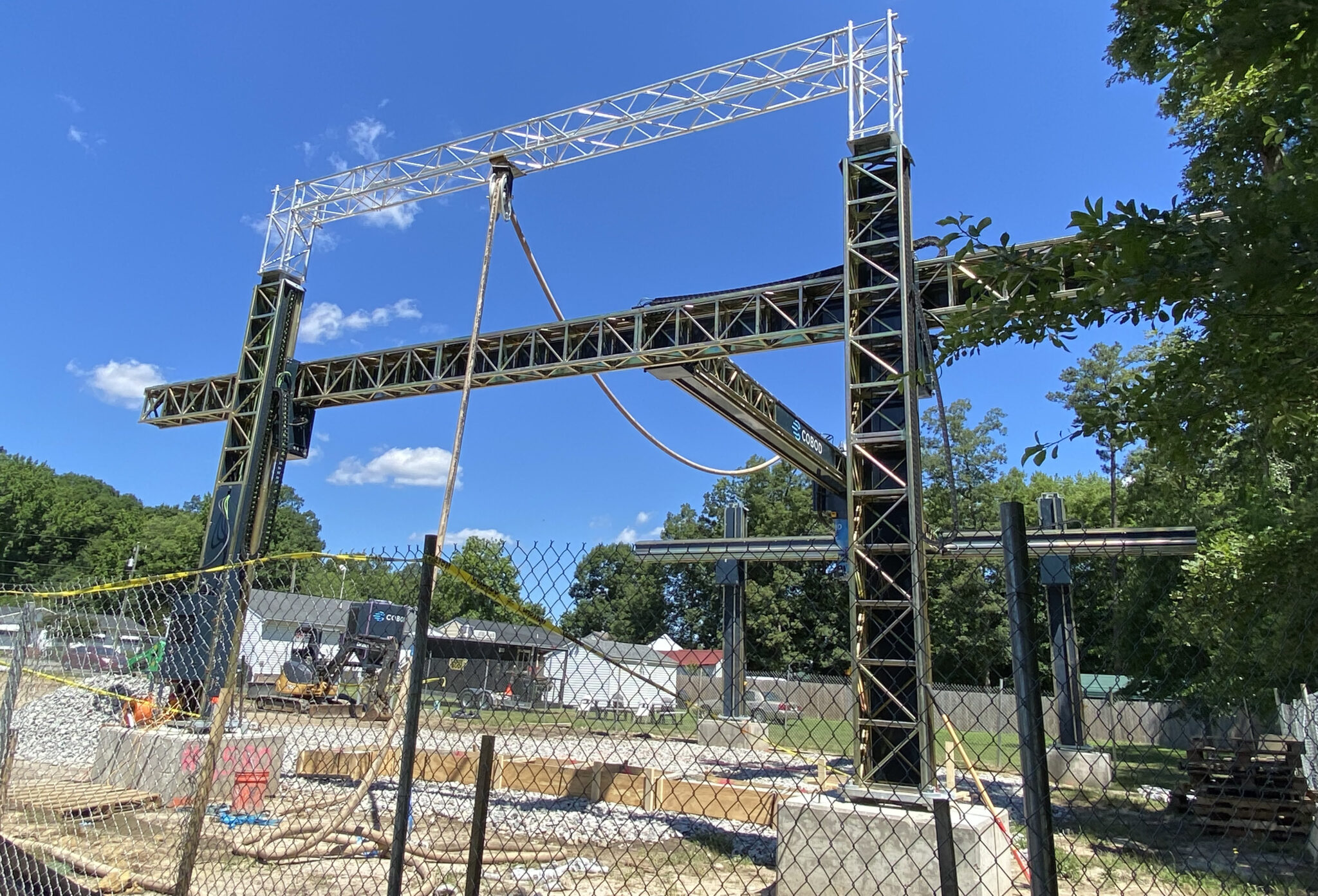
The large-scale 3D printer’s frame is massive. It is one of only two in the U.S. that prints with concrete.
By reducing the amount of time spent on a job site, Thompson said, you can also reduce costs like insurance and carrying fees. It also reduces the amount of contract labor — you can use fewer people to get the same amount and same quality of work done.
Thompson said their theory is that the 3D printing could save a loosely estimated 10 percent of overall construction costs.
The house will also be outfitted with a system that will monitor energy consumption and moisture levels — among many other things — and will relay the information back to Virginia Housing so they can improve the printing process in the future.
The house at 217 Carnation St. is expected to be just under 1,600 square feet and will be on the market at around $200,000. Richmond nonprofits Better Housing Coalition and project:HOMES will handle the sale of the house.
Better Housing Coalition and project:HOMES initially identified the land for the construction effort and will later be identifying the buyer who will have the option to secure a mortgage through Virginia Housing. The property is currently owned by project:HOMES.
Despite this being an experimental project, Thompson said that they have multiple other projects lined up for the printer if the Carnation Street home goes well. That includes a partnership with a Habitat For Humanity affiliate in James City County and a small subdivision of homes in Exmore, Virginia.
Whether it takes off could depend on the construction industry’s willingness to adopt this sort of new technology, Thompson said.
“We’re in an industry that’s used to tradition. There hasn’t been a lot of innovation in homebuilding over time,” he said.
Thompson added, “We’ve seen this technology take off in other parts of the world, particularly in parts of Europe and the Middle East, where it’s used in greater productions. We look forward to doing this on a much broader scale.”